一、引言
立式化工管道离心泵作为化工领域中不可或缺的流体输送设备,在各类化工生产过程中发挥着关键作用。它能够高效、稳定地输送各种具有不同特性的化工流体,从腐蚀性较强的酸液到高粘度的有机溶液等。深入了解其工作原理和性能特点,对于化工工程师进行设备选型、系统设计以及日常运行维护都具有至关重要的意义。通过对其工作原理的剖析,可以更好地理解设备如何将电能转化为流体的动能和势能,实现流体的定向输送;而对性能的研究,则有助于在实际应用中充分发挥设备的优势,提高生产效率,降低能耗,并确保整个化工生产过程的安全与稳定。
二、立式化工管道离心泵的工作原理
(一)基本结构
立式化工管道离心泵主要由泵体、叶轮、泵轴、电机、密封装置等部件组成。泵体通常采用高强度的金属材料制造,如不锈钢、碳钢等,以承受化工流体的压力和腐蚀作用。叶轮是离心泵的核心部件,它一般由多个弯曲的叶片构成,安装在泵轴上。泵轴将电机的动力传递给叶轮,使其高速旋转。电机为离心泵提供旋转动力,通常选用符合化工环境要求的防爆电机或普通电机。密封装置则用于防止化工流体泄漏,常见的密封形式有机械密封和填料密封,机械密封具有密封性能好、泄漏量小等优点,在化工离心泵中应用广泛。
(二)工作过程
吸入过程
当电机启动后,泵轴带动叶轮高速旋转。叶轮内的流体在离心力的作用下,从叶轮中心被甩向叶轮边缘,使叶轮中心形成低压区。此时,泵入口处的化工流体在外界大气压或系统压力的作用下,沿着吸入管道进入叶轮中心,填补被甩走的流体所留下的空间。这个过程中,流体的静压能逐渐转化为动能,速度不断增加。
排出过程
随着叶轮的持续旋转,被吸入叶轮的化工流体在离心力的作用下继续向叶轮边缘流动。在这个过程中,流体的速度进一步提高,动能不断增大。当流体到达叶轮边缘时,具有较高的速度和动能。高速流体进入泵体的蜗壳形流道后,由于流道的截面积逐渐增大,流体的流速逐渐降低,动能又部分转化为静压能,使流体的压力进一步升高。最终,具有较高压力的流体通过泵的出口管道被输送到需要的地方,完成整个排出过程。
(三)理论基础
离心力原理
离心力是立式化工管道离心泵工作的关键理论依据。根据牛顿第二定律,当物体做圆周运动时,会受到一个指向圆心的向心力作用,同时物体也会产生一个大小相等、方向相反的离心力。在离心泵中,叶轮高速旋转时,流体在叶轮内做圆周运动,受到离心力的作用被甩向叶轮边缘。离心力的大小与流体的质量、叶轮的旋转角速度以及流体到叶轮中心的距离成正比。因此,叶轮的转速越高,流体所受到的离心力就越大,能够获得的动能也就越大,从而可以实现更高扬程的流体输送。
伯努利方程
伯努利方程描述了理想流体在定常流动过程中,流体的压力能、动能和势能之间的转换关系。在立式化工管道离心泵的工作过程中,伯努利方程同样适用。在吸入过程中,流体从入口进入叶轮中心,压力逐渐降低,速度逐渐增加,即压力能转化为动能;在排出过程中,流体从叶轮边缘进入蜗壳流道,速度逐渐降低,压力逐渐升高,动能又转化为压力能。通过对伯努利方程的应用,可以更深入地分析离心泵内部流体的能量转换过程,为泵的设计和性能优化提供理论支持。
三、立式化工管道离心泵的性能参数
(一)流量(Q)
流量是指单位时间内通过泵出口的流体体积,通常用立方米每小时(m³/h)或升每秒(L/s)来表示。流量是衡量离心泵输送能力的重要指标之一。它受到多种因素的影响,包括叶轮的尺寸、转速、泵的结构形式以及所输送流体的性质等。在一定的转速下,叶轮直径越大,泵的流量通常也越大。流量与泵的扬程之间存在一定的关系,一般来说,随着流量的增加,泵的扬程会逐渐降低。
(二)扬程(H)
扬程是指单位重量的流体通过泵后所获得的能量增加值,单位为米(m)。它反映了泵能够将流体提升的高度或克服管道阻力的能力。扬程包括吸水扬程和压水扬程两部分。吸水扬程是指泵能够从低处将流体吸入的高度,而压水扬程是指泵能够将流体压送到高处的高度。扬程的大小取决于叶轮的形状、尺寸、转速以及流体的密度等因素。在实际应用中,需要根据具体的输送要求来选择合适扬程的离心泵。
(三)转速(n)
转速是指泵轴每分钟的旋转次数,单位为转每分钟(r/min)。转速是影响离心泵性能的重要参数之一。根据离心泵的相似定律,在同一台泵中,流量与转速成正比,扬程与转速的平方成正比,功率与转速的立方成正比。因此,通过改变转速可以调节泵的流量、扬程和功率,以满足不同的工作需求。在实际运行中,可以采用变频调速等技术来实现对离心泵转速的精确控制。
(四)功率(P)
功率是指离心泵在运行过程中所消耗的能量,分为轴功率和有效功率。轴功率(Pa)是指电机传递给泵轴的功率,也就是泵实际所消耗的功率,单位为千瓦(kW)。有效功率(Pe)是指单位时间内通过泵的流体所获得的能量,计算公式为 Pe = ρgQH/1000,其中 ρ 为流体的密度(kg/m³),g 为重力加速度(m/s²),Q 为流量(m³/s),H 为扬程(m)。泵的效率(η)等于有效功率与轴功率之比,即 η = Pe/Pa×100%。效率反映了泵对能量的利用程度,是衡量泵性能优劣的重要指标之一。一般来说,离心泵的效率在 60% - 85%之间,不同类型和规格的泵效率会有所差异。
(五)汽蚀余量(NPSH)
汽蚀余量是指在泵入口处,单位重量流体所具有的超过汽化压力的富余能量,单位为米(m)。它是衡量泵抗汽蚀性能的重要指标。当泵入口处的压力低于流体的汽化压力时,流体就会发生汽化,产生大量的气泡。这些气泡随着流体进入叶轮高压区时,会迅速破裂,形成局部的高压冲击,对叶轮和泵体造成损坏,这种现象称为汽蚀。为了避免汽蚀现象的发生,泵的安装高度和吸入管道的设计必须保证泵入口处的汽蚀余量大于泵的必需汽蚀余量。必需汽蚀余量与泵的结构、转速、流量等因素有关,一般由泵的制造商提供。
四、影响立式化工管道离心泵性能的因素
(一)流体性质
密度
流体的密度对离心泵的性能有一定影响。密度越大,在相同的流量和扬程下,泵所需要的轴功率就越大。这是因为密度大的流体具有更大的质量,在输送过程中需要更多的能量来克服阻力和提升高度。例如,输送密度较大的浓硫酸与输送水相比,在相同的工况下,输送浓硫酸的离心泵需要更大功率的电机
粘度
粘度是反映流体内部阻力的物理量。当流体的粘度增加时,流体在泵内的流动阻力增大,导致泵的流量和扬程下降,轴功率增加。粘度的增大还会影响泵内流体的流动状态,使泵的效率降低。对于高粘度流体的输送,通常需要选用特殊设计的离心泵,如螺杆泵等,或者对普通离心泵进行适当的改造,以提高其对高粘度流体的适应性
腐蚀性
化工生产中所涉及的许多流体具有腐蚀性,如酸、碱等溶液。这些腐蚀性流体可能会对泵的材料造成侵蚀,导致泵体、叶轮等部件的损坏,从而影响泵的性能和使用寿命。为了应对流体的腐蚀性,需要选用合适的耐腐蚀材料来制造泵的部件,如不锈钢、钛合金等,或者在泵的表面进行防腐处理,如涂覆防腐涂料等。
(二)泵的结构
叶轮形状
叶轮的形状对离心泵的性能有重要影响。常见的叶轮形状有闭式叶轮、半闭式叶轮和开式叶轮。闭式叶轮的效率较高,适用于输送清洁、无颗粒的流体;半闭式叶轮适用于输送含有少量颗粒的流体;开式叶轮则适用于输送含有较多颗粒或纤维的流体。不同形状的叶轮在流量、扬程和效率等方面表现出不同的特性。例如,闭式叶轮在相同的工况下,其扬程和效率通常比开式叶轮要高。
蜗壳设计
蜗壳是离心泵的重要组成部分,它的设计直接影响流体在泵内的流动状态和能量转换效率。合理的蜗壳设计可以使流体在离开叶轮后能够平稳地流动,减少能量损失,提高泵的扬程和效率。蜗壳的截面积、形状以及与叶轮的匹配等因素都会对泵的性能产生影响。例如,蜗壳的截面积过小会导致流体在蜗壳内的流速过高,增加能量损失;而截面积过大则会使流体在蜗壳内的停留时间过长,也会降低能量转换效率。
(三)运行工况
流量调节
在实际运行中,常常需要根据生产需求对离心泵的流量进行调节。常见的流量调节方法有改变阀门开度、改变泵的转速和切削叶轮等。改变阀门开度是一种简单易行的调节方法,但会增加管道系统的阻力,导致泵的能耗增加;改变泵的转速可以在不增加管道阻力的情况下实现流量调节,且调节范围较大,节能效果明显;切削叶轮则是一种通过改变叶轮直径来调节流量的方法,适用于长期稳定的流量调节需求,但这种方法会使泵的性能曲线发生改变,需要谨慎使用。
安装高度
泵的安装高度对其性能也有重要影响。如果安装高度过高,泵入口处的压力可能会过低,导致流体发生汽化,产生汽蚀现象,从而损坏泵的部件,降低泵的性能。因此,在安装离心泵时,必须根据泵的必需汽蚀余量、当地的大气压力以及所输送流体的性质等因素,合理确定泵的安装高度,以确保泵能够正常运行。
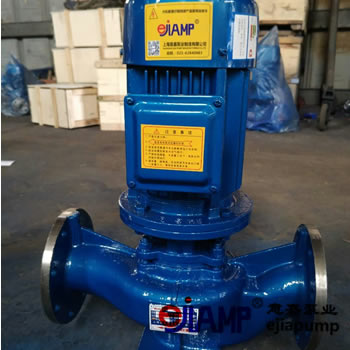
相关产品
意嘉泵业其他产品:管道泵 多级离心泵 磁力泵 排污泵 化工泵 螺杆泵 多级泵 隔膜泵 自吸泵 油桶泵 齿轮油泵 计量泵 屏蔽泵 离心泵 潜水泵 深井泵 塑料泵 氟塑料泵 液下泵 漩涡泵 纸浆泵 玻璃钢泵 转子泵 管道离心泵 浓浆泵 消防泵 水泵控制柜 污水泵 成套给水设备